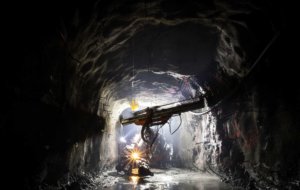
Drilling techniques in mining: What is possible?
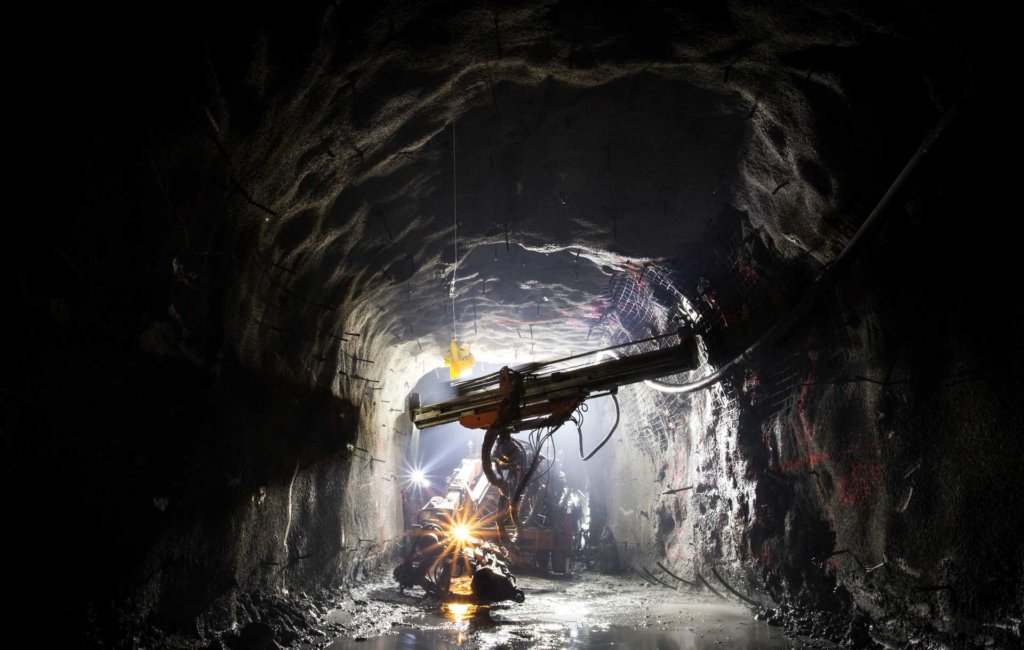
Mineral exploration in mining naturally involves drilling to discover what is below the surface. While there have been a number of innovations in drilling technologies in the petroleum and geothermal sectors, there have been no significant advances in mineral drilling technology in the mining sector for decades. Generally, mineral exploration involves percussion and rotary drilling to obtain rock chips and core samples.
Drilling is used to obtain detailed information on rock types, mineral content, rock structure, and the relationship between rock layers near the surface and at depth. They are used in areas selected on the basis of geological, geophysical and/or geochemical methods.
The different drilling techniques
There are three primary techniques that can be used for mineral exploration. The selection of a particular method depends on a number of factors, for example, in terms of cost, environment, type of equipment needed, and the skills and knowledge of those involved.
Rotating air jets
Rotary air blasting is both the least expensive and the simplest technique for mining exploration. The technique also requires limited knowledge, but it is not without drawbacks. Therefore, rotary airblasting is generally not preferred for mining exploration because it is not possible to obtain a representative sample using rotary airblasting.
Rotary air blasting, or rotary blowing, is a type of rotary drilling that uses a blade bit or roller cone bit to cut and break rock with a simple blade mounted on the end of a rotating drill rod. This shaft is rotated while a thrust is applied to it by a trigger mechanism that uses up to 65 percent of the machine’s weight. While the bit breaks and removes the rock, either by crushing and chipping or by plowing and scraping, compressed air is supplied to the bit. The air cools the bit and flushes the cuttings back to the surface.
In this method, air is injected by a compressor through the upper swivel joint of a rotary head. When the compressed air returns to the surface, it takes with it the rock chips produced by the rotating bit. It is used in soft rock material up to a depth of about 25 meters. Drilling can be done through the top layer of decomposed rock and soil to obtain a fresh rock sample from the underlying bedrock. Typically, a piece of line pipe is set at the surface to prevent erosion at the top of the borehole. Drill cuttings and air are then returned from the annular space between the drill pipe and the borehole wall upwards from the bit face to the surface.
Reverse circulation well
Reverse circulation drilling, also called RC drilling, is more expensive than rotary blowing. In addition, the process requires more equipment and greater expertise. However, RC drilling also results in greater sample accuracy, making it a more popular form of mining drilling techniques. RC drilling is the most widely used drilling technique for mining exploration in the world.
RC drilling is a form of percussion drilling in which the rock is caused to fracture by the use of a piston that delivers rapid blows to the drill shaft, transferring appropriate energy to the drill bit. These blows to the rock are delivered by the bit, while a rotating device ensures that the bit hits a new rock surface with each blow. A feed force is applied to maintain contact between the rock and the bit. In addition, compressed air is used to remove the drill cut from the hole and efficiently advance the drilling depth.
RC drilling uses a double-walled drill pipe. The air is injected between the two pipes and exits the drill pipe behind the bit. The air and cuttings are forced over the face of the bit and back into the inner tube. From there, air and cuttings are returned to the surface and to the top of the rotary head via a baffle and drain hose.
Diamond core drilling
As with RC drilling, diamond core drilling requires a high level of expertise and skill. Diamond core drilling requires less equipment than RC drilling, but is more expensive because it is a time-consuming process that takes about five times as long as RC drilling to drill an equivalent amount of rock. When using diamond core drilling, there are additional costs for drill bits, drilling aids, fuel and labor.
Diamond core drilling uses a tube set with industrial diamonds to drill through rock strata. A core of rock remains in the middle of the tube, which is then taken as a sample. This core can then be analyzed to learn more about its composition as well as the relationship between the rock layers.
Diamond core drilling requires a high speed of 300 to 1200 rpm, while keeping the weight and penetration depth constant to ensure that the core is not washed away. Diamond core drilling requires a high degree of skill, since in hard rock formations too much weight can cause the core bit to burn, while too little weight can risk blunting the core bit. An experienced operator knows what type of drill to use and how much weight to apply.
There are two ways in which samples can be taken from a diamond drill bit. Conventional coring requires the entire core barrel to be pulled to the surface, which means that all drill rods must be pulled out of the hole. Wire-line coring involves raising the inner pipe to the surface and lowering it back into the pipe with a winch through the drill pipe. This saves time because the drill pipe remains in the hole. In wire-line coring, the equipment consists of a high-speed rotary unit running at over 1000 rpm, a feed system that applies uniform and constant pressure to the bit, and a diesel engine to drive the unit. The drill pipe is handled manually because the drill pipes are shorter and lighter than in rotary drilling. Core drills are equipped with a water pump to flush the cuttings between the hole wall and drill pipe to the surface.
Which drilling technique should be used and when?
In mining, drilling techniques can be used to determine information about rock types, mineral content and more. There are a number of considerations that should be weighed when deciding which method to use:
- Rotary air jetting is most commonly used for site investigations, environmental and geotechnical drilling, and sampling into weathered and poorly consolidated material to obtain a soil sample. It can also be used to obtain a fresh rock sample from bedrock under decomposed rock and soil.
- For hard rock types, reverse core drilling (RC drilling) can be used to penetrate to depths of several hundred meters, both for exploration and blasting. RC drilling allows for uncontaminated chip samples and can be used in all formation types. While they are more expensive and require more equipment, their accuracy makes them one of the most popular drilling techniques for mining exploration.
- Diamond core drilling is best used in consolidated formations. Compared to rotary drills, diamond core drills are small and well suited for remote exploration sites. Diamond core drilling provides intact samples, but is more expensive than other drilling techniques.
With an experienced project manager, the appropriate drilling technology can be selected to best define the parameters of a drilling project.