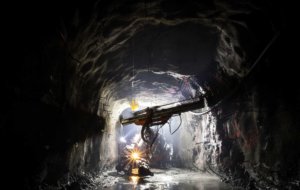
Tunneling: What are the drilling methods?
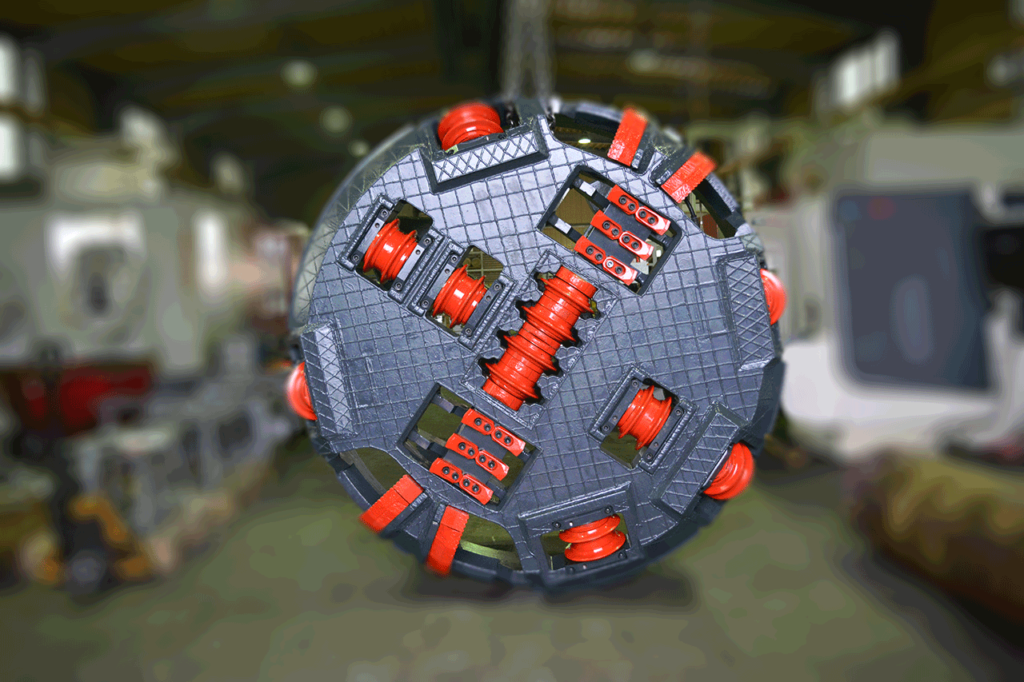
For the construction of a new underground tunnel, special tunnel boring machines are used in almost all cases today. Depending on individual requirements, different drilling methods can be used.
Things to know about the tunnel boring machine
A tunnel boring machine (TBM) – also called a “mole” – is a complex machine used to create tunnels, usually with a circular cross-section (other cross-sections are also possible), through various layers of soil and rock. It can also be used for so-called microtunneling.
Tunnel boring machines can be designed to work in any material – from hard rock to loose sand. The achievable tunnel diameters can range from one meter (performed with micro-TBM) to almost 20 meters. Tunnels with a diameter of less than one meter are usually not constructed with a tunnel boring machine, but with trenchless construction methods or horizontal directional drilling. Tunnel boring machines, as mentioned, can also be designed for driving tunnels with non-circular cross-sections, e.g. U-shaped or horseshoe-shaped as well as square or rectangular tunnels.
Tunnel boring machines can be used as an alternative to drilling and blasting in rock as well as to conventional hand mining. They have the advantage of limiting the load on the surrounding soil and creating a smooth tunnel wall that can be lined directly. This significantly reduces the cost of lining the tunnel and makes them suitable for use in heavily built-up areas.
The biggest disadvantage is the comparatively high upfront costs. Tunnel boring machines are very expensive to manufacture and require high transportation costs. In general, the longer the tunnel, the lower the cost of using a tunnel boring machine compared to conventional drilling and blasting methods. The reason: tunneling with special drilling machines is much more efficient and entails shorter completion times. Only in the case of highly fractured, sheared rock strata should the conventional drill and blast method be preferred.
The modern tunnel boring machine
Modern tunnel boring machines typically consist of a rotating cutting wheel, the so-called cutting head, followed by a main bearing, a feed system and the trailing support mechanisms. Which type of machine is used depends on the particular geology of the project, the amount of groundwater present, and various other factors.
The main drilling methods and designs of tunnel boring machines are:
Hard Rock Tunnel Boring Machines
In hard rock, either shielded or open tunnel boring machines can be used. Hard rock tunnel boring machines excavate the rock with disc cutters mounted in the cutter head. The disc cutters create compressive stress fractures in the rock, causing it to break off. The removed rock (debris) is fed through openings in the cutting head onto a conveyor belt, where it passes through the machine to a system of conveyor belts or debris carts for removal from the tunnel.
Open tunnel boring machines do not have a shield, leaving the area behind the boring head open for rock support. To advance, the machine uses a gripper system that presses against the tunnel walls. Not all machines can be steered continuously while the gripper shoes press against the walls.
In the open tunnel boring machine, concrete segments are not installed one after the other as in other machines. Instead, the rock is supported using ground support methods such as ring beams, rock bolts, shotcrete, steel straps, ring steel, and wire mesh.
Tunnel boring machines with shield drive
In fractured rock, shielded hard rock tunnel boring machines can be used to erect concrete segments to support unstable tunnel walls behind the machine. Double shield tunnel boring machines have two modes of operation. In stable ground, they grip against the tunnel walls to ensure propulsion; in unstable ground, the thrust is shifted to thrust cylinders that brace against the tunnel segments behind the machine. This can prevent the shear forces from acting on the unstable tunnel walls. Single shield drills work in the same way, but are used only in unstable soil.
Soft bottom tunnel boring machines
In soft soils, there are three main types of tunnel boring machines: earth pressure equalization machines, slurry shield machines and open machines. Both types of enclosed machines operate like single-shield tunnel boring machines and use thrust cylinders to move forward by pushing against concrete segments. Earth pressure equalization machines are used in soft soil with less than 7 bar pressure. The cutter head uses not only disc cutters, but a combination of carbide bits, carbide disc cutters, drag bits, and/or hard rock disc cutters.
The earth pressure equalization machine gets its name because it uses the excavated material to equalize the pressure. Pressure is maintained in the cutting head by controlling the rate of overburden conveyance through the Archimedean screw and the feed rate. Additives such as bentonite, polymers and foam can be injected to increase the stability of the soil. Additives can also be introduced into the cutting head/auger to ensure that the excavated material remains sufficiently cohesive to form a plug in the Archimedes auger, maintain pressure in the cutting head, and limit water flow.
In soft soils with very high water pressure or in granular soil conditions (sands and gravels), when a plug cannot be formed in the Archimedes auger, Slurry Shield tunnel boring machines are required. The cutting head is filled with a pressurized suspension that exerts hydrostatic pressure. The slurry also serves as a transport medium, mixing with the excavated material before being pumped from the drill head back to a slurry separation unit, usually located outside the tunnel.
Sludge separation plants are multi-stage filtration systems that remove overburden particles from sludge so that it can be reused in the construction process. The limit to which sludge can be cleaned depends on the particle size of the excavated material. For this reason, slurry tunnel boring machines are not suitable for silts and clays, because the particle sizes of the excavated material are smaller than necessary.
In soft ground, open tunnel boring machines rely on the working face – the point where the advance takes place – to straighten up for a short time without support. This makes them suitable for use in rock types with a strength of up to approx. 10MPa and with low water inflows.
While there is no need for a large number of workers operating at high pressure at the face when using conventional tunnel boring machines, slurry shield TBMs often use a caisson system at the cutting head. formed. Workers entering this space for inspection, maintenance, and repair must be medically cleared as “fit for diving” and trained in the operation of the airlocks.