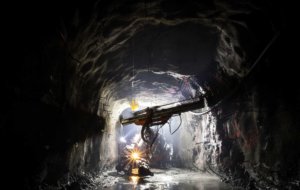
Surface hardening in metal construction - how and what?
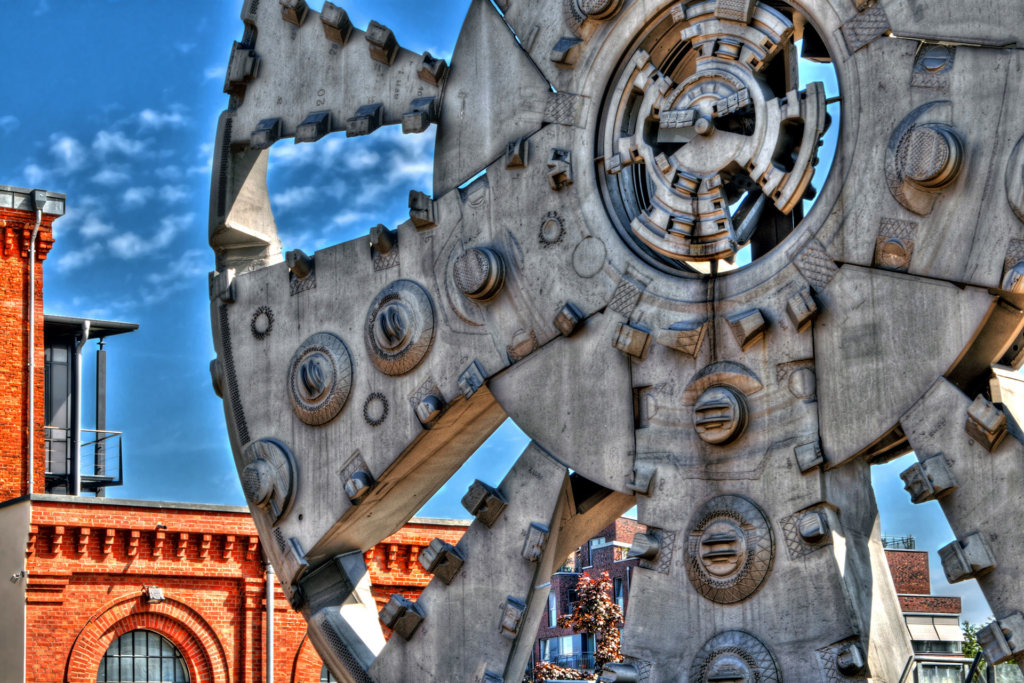
Case hardening, or surface hardening, involves hardening the surface of a metal object while leaving the underlying metal soft, so that a thin layer of harder metal (called an “insert”) forms on the surface. For iron or steel with low carbon content, which by itself has poor to no hardenability, additional carbon or nitrogen is introduced into the surface layer during case hardening. Case hardening is usually performed after the part has been formed into its final shape.
Hardening is desirable for metal parts subjected to sliding contact with hard or abrasive materials because the hardened metal is more resistant to surface wear. However, since hardened metal is generally more brittle than softer metal, through-hardening (i.e., hardening the metal uniformly throughout the part) is not always an appropriate choice. In such circumstances, case hardening can produce a part that does not fracture (because of the soft core that can absorb stresses without breaking), but also provides adequate wear resistance at the hardened surface.
Chemical process
The carbon itself is solid at case hardening temperatures and thus immobile. Transport to the steel surface occurs as gaseous carbon monoxide produced by the decomposition of the carburizing compound and the oxygen trapped in the closed environment. This is done with pure carbon, but too slowly to be processable. Although oxygen is required for this process, it is recycled through the CO loop and therefore can be performed in a sealed environment. Sealing is necessary to prevent the CO from either leaking or being oxidized to CO2 by excess outside air.
Both carbon and alloy steels are suitable for case hardening; typically, mild steels with low carbon content, usually less than 0.3%, are used. These unalloyed steels are normally not hardenable due to the small amount of carbon, so the surface of the steel is chemically altered to increase hardenability. Case-hardened steel is produced by diffusing carbon (carburization), nitrogen (nitriding) and/or boron (boronization) into the outer layer of the steel at high temperature, followed by heat treatment of the surface layer to the desired hardness.
The term case hardening is derived from the practicalities of the carburizing process, which is essentially the same as the old process. The steel workpiece is surrounded by a carbon-releasing medium – this is generally referred to as carburizing. The workpiece is placed in a hot oven for a variable period of time. Time and temperature determine how deep the curing extends into the surface. However, the depth of hardening is ultimately limited by the inability of the carbon to diffuse deeply into the solid steel. A typical depth of surface hardening using this method is up to 1.5 mm. Modern carburizing also uses other techniques, such as heating in a carbon-rich atmosphere. Small parts can be case hardened by repeated heating with a torch and quenching in a carbon-rich medium.
Different processes of surface hardening
Flame or induction hardening
Flame or induction hardening are processes in which the steel surface is heated very rapidly to high temperatures (by direct application of an oxygen gas flame or by induction heating) and then rapidly cooled again, generally using water. A carbon content of 0.3-0.6% by weight C is required for this type of hardening.
Typical applications include the shackle of a lock, where the outer layer is hardened to be fire resistant, and mechanical gears, where hard gear meshing surfaces are needed to provide long life, while toughness is required to provide durability and resistance to breakage.
Nitriding
In nitriding, the steel part is heated to 482 – 621 °C in an atmosphere of ammonia gas and dissociated ammonia. The time the part spends in this environment determines the depth of cure. The hardness is achieved by the formation of nitrides. For this process to work, nitride-forming elements must be present. These elements include chromium, molybdenum and aluminum. The advantage of this process is that it causes little distortion. No quenching is performed after nitriding.
Cyanize
Cyanizing is a fast and efficient case hardening process. It is mainly used for steels with low carbon content. The part to be cured is heated to 871 – 954 °C in a sodium cyanide bath, then quenched and rinsed in water or oil to remove all cyanide residues.
This process produces a thin, hard surface layer (between 0.25 and 0.75 mm) that is harder than that produced by carburizing, and can be completed in 20 to 30 minutes, giving parts less opportunity to warp. It is typically used on small parts such as bolts, nuts, screws and small gears. The main disadvantage of cyanidation is that cyanide salts are toxic. Appropriate occupational safety is therefore absolutely necessary.
Carbonitriding
Carbonitriding is similar to cyanization, except that a gaseous atmosphere of ammonia and hydrocarbons is used instead of cyanide. If the part is to be quenched, it is heated to 775 – 885 °C; if not, the insert temperature is 649 – 788 °C.
Nitrocarburieren
During (ferritic) nitrocarburizing, mainly nitrogen and some carbon diffuse into the surface layer of a workpiece below the critical temperature of approx. 650 °C. The carbon is then released into the surface layer. Below the critical temperature, the microstructure of the workpiece does not transform into an austenitic phase but remains in the ferritic phase, which is why the process is also known as ferritic nitrocarburizing.
General applications of surface hardening
Parts subjected to high pressures and sharp impacts are still usually case hardened. Examples include firing pins and rifle bolt faces or engine camshafts. In these cases, the surfaces that need the hardening can be selectively hardened while leaving the majority of the part in its original, tough state.
Another common application of case hardening involves screws, especially self-drilling screws. In order for the screws to cut into other materials such as steel, the drill tip and the threads that form must be harder than the material or materials being drilled into. However, if the entire screw is uniformly hard, it becomes very brittle and breaks easily. This is overcome by ensuring that only the surface is hardened and the core remains relatively soft and therefore less brittle. For screws and fasteners, case hardening is achieved by a simple heat treatment consisting of heating followed by quenching.